FASTEC® system
Performs punching, stacking, measurement, and assembly inside the die. Supports three stacking methods to enable the manufacturing of optimal motors.
By leveraging its cutting technology used for manufacturing spline gauges and precision tools, KURODA introduced its lamination press die for motor cores known as the “FASTEC® system” in 1976.
This system brought dramatic improvement to quality and productivity since it allowed for processing all operations from punching to stacking, measurement, and assembly within the stamping process.
It allows you to accurately and efficiently manufacture optimal motor cores that meet your needs in an era requiring high-efficiency motors with excellent energy-saving characteristics.
We are able to produce optimal motor cores to meet customer needs by three types of lamination methods.
FASTEC (Concavity stacking)
Feature:Low cos, many know-how and handle to various shape
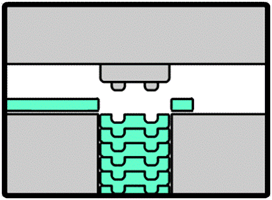
Many adopted there HEV Maine motor core.
LASER FASTEC® (Spot welding stacking)
Features: Specialized for very small workpieces. Achieves reliable stacking force even in very small shapes.
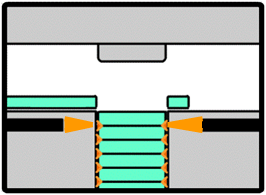
LASER FASTEC® is a technology developed to mass-manufacture high-precision, tiny thin laminated products. The use of YAG laser to firmly fasten metal sheets enables LASER FASTEC® to be less restricted to product shapes it can handle, making it possible to mass-manufacture tiny thin laminate products with stable strength and quality, which was traditionally considered difficult. We accept orders for custom metal press products manufactured to customers’ standards.
Glue FASTEC® (Glue stacking)
Features: Ideal for very thin laminates! Achieves highly efficient, high-quality, and high-precision motor cores.
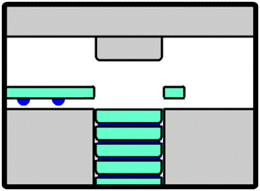
Glue FASTEC® is a ground-breaking system which, by using glue to firmly fasten metal sheets, made it possible to automatically stack metal sheets inside the die while keeping the insulated condition. We accept orders for custom stamped products manufactured to customers’ standards.